A Panel Tracking System For The Mining Industry
Industries face the problem of wear and tear and the necessity to replace their machines and spare components.
Project Description
It is crucial to determine the cause of the wear and tear.
To prevent delays in the process of production It is essential to maintain the stock of spare parts and raw materials up-to-date.
In the top mining firm within South Africa, inventory and wear and tear information were maintained using Excel. The process was not structured long, it was time-consuming, and did not give a clear picture of the whole process.
We at Qualy5 developed an ERP dashboard and mobile application that gives the supervisors a 360-degree overview of the system provides timely alerts and helps them save time and effort.

Background
Iron ore is processed through large mechanical screens that remove large particles of ore from the finer dust. The screens are outfitted with panels that endure mechanical stress, fatigue strains and damage caused by shocks, welding etc.
It’s crucial to determine the cause of the damage and the exact place of the panel which is damaged.
If the data is collected and analysed this data could make mining companies save thousands of dollars per month by delaying the source of the harm and minimizing the extent of it.
Challenges Faced
Challenges 1
It is still possible to keep data from printed forms, you can also incorporate them into the software. However, paper forms are difficult to maintain and require conversion of data to digital formats and are often lost. This leads to missing data elements that are crucial for achieving the desired results.
Challenges 2
The data can be collected by using the Excel spreadsheet. But, the data isn’t centralized and it is difficult to enter. In addition, it’s hard to analyse and interpret the data in an Excel spreadsheet.
Challenges 3
It’s difficult to see and interpret the screen’s data points in Excel spreadsheets.
The Proposed Solution
The solution has 3 modules
Module 1
An app for tablets and the mobile phone that permits quick identification of and reports on the damage to panels. The information entered is stored in the cloud.
Module 2
Cloud-based service that manages and stores information and gives valuable insight.
Module 3
Alert and notifications of low stock Regular replacements
Results
Result 1
Software that is intuitive, secure, and simple to use in daily operations.
Result 2
It is a clean, organized, and informative dashboard that provides easy access to deep insights and allows for quick decisions.
Result 3
An alert system that informs you before the inventory ends.
Result 4
A heat map that highlights the areas that need attention.
Overview Of Technologies Used
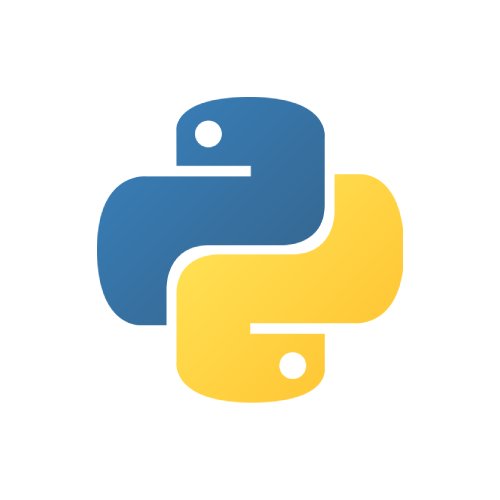
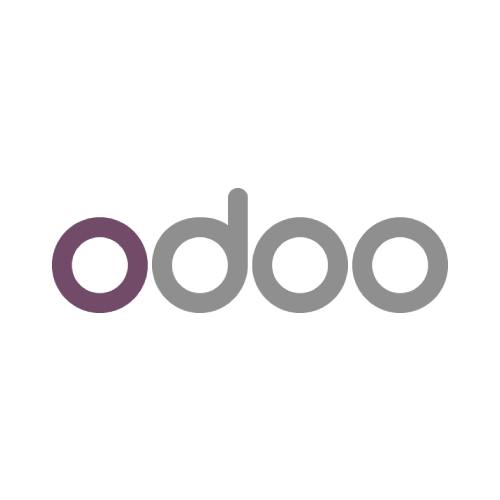
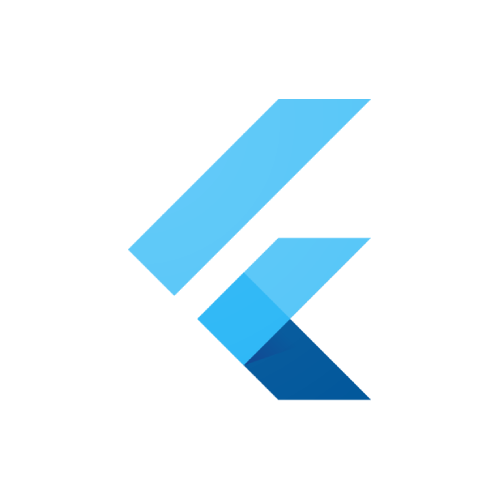
Web Application Overview
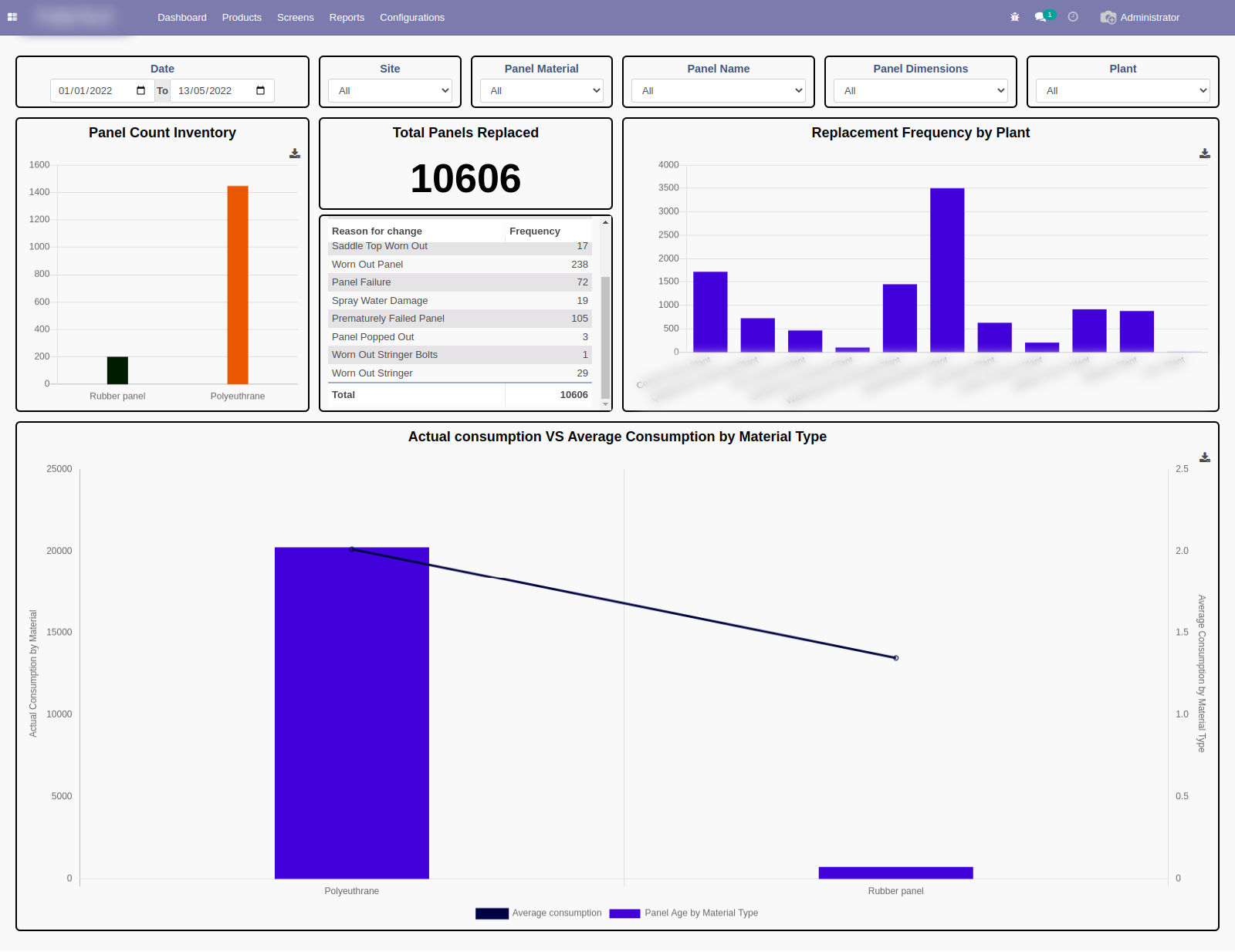
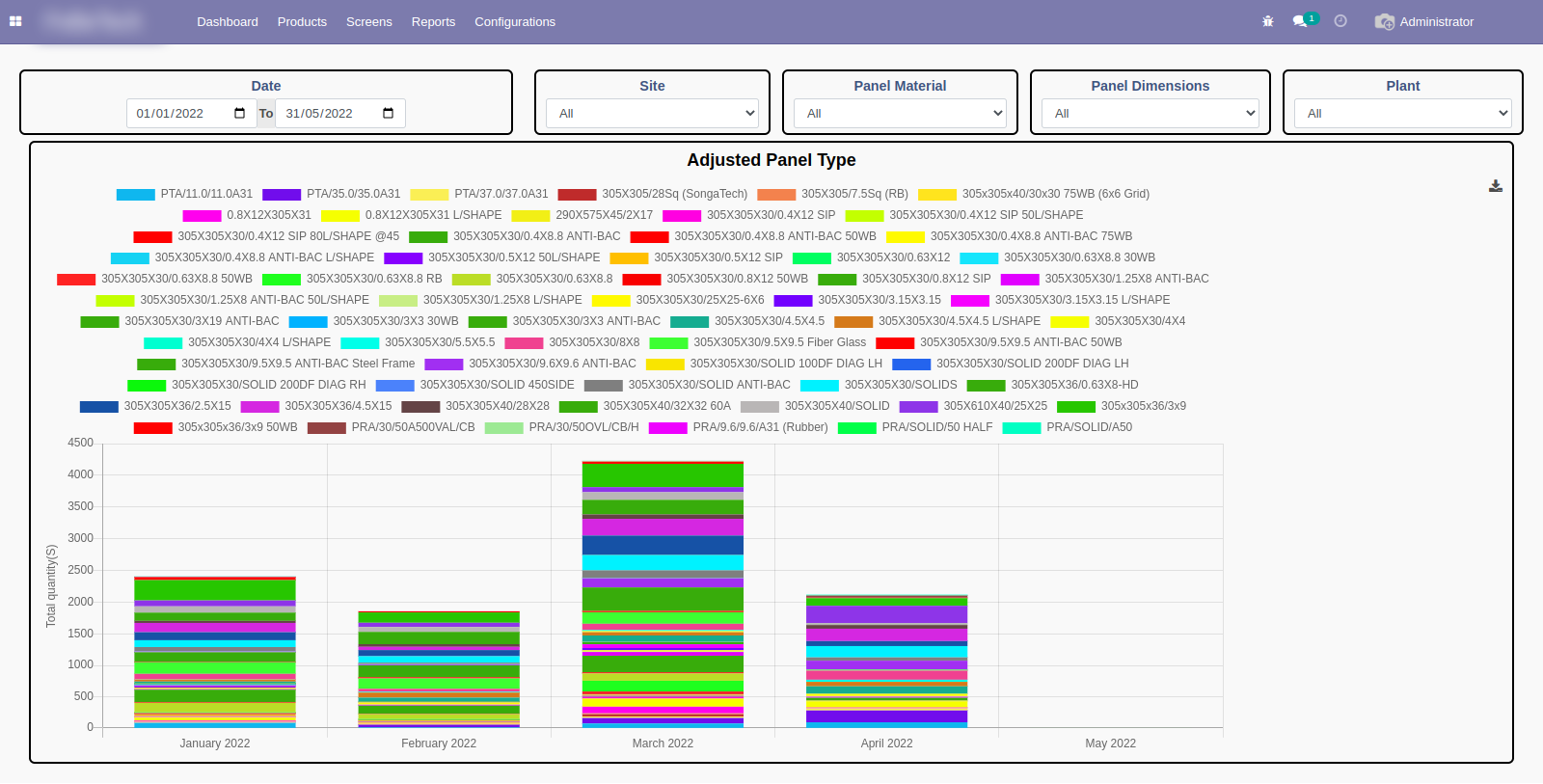
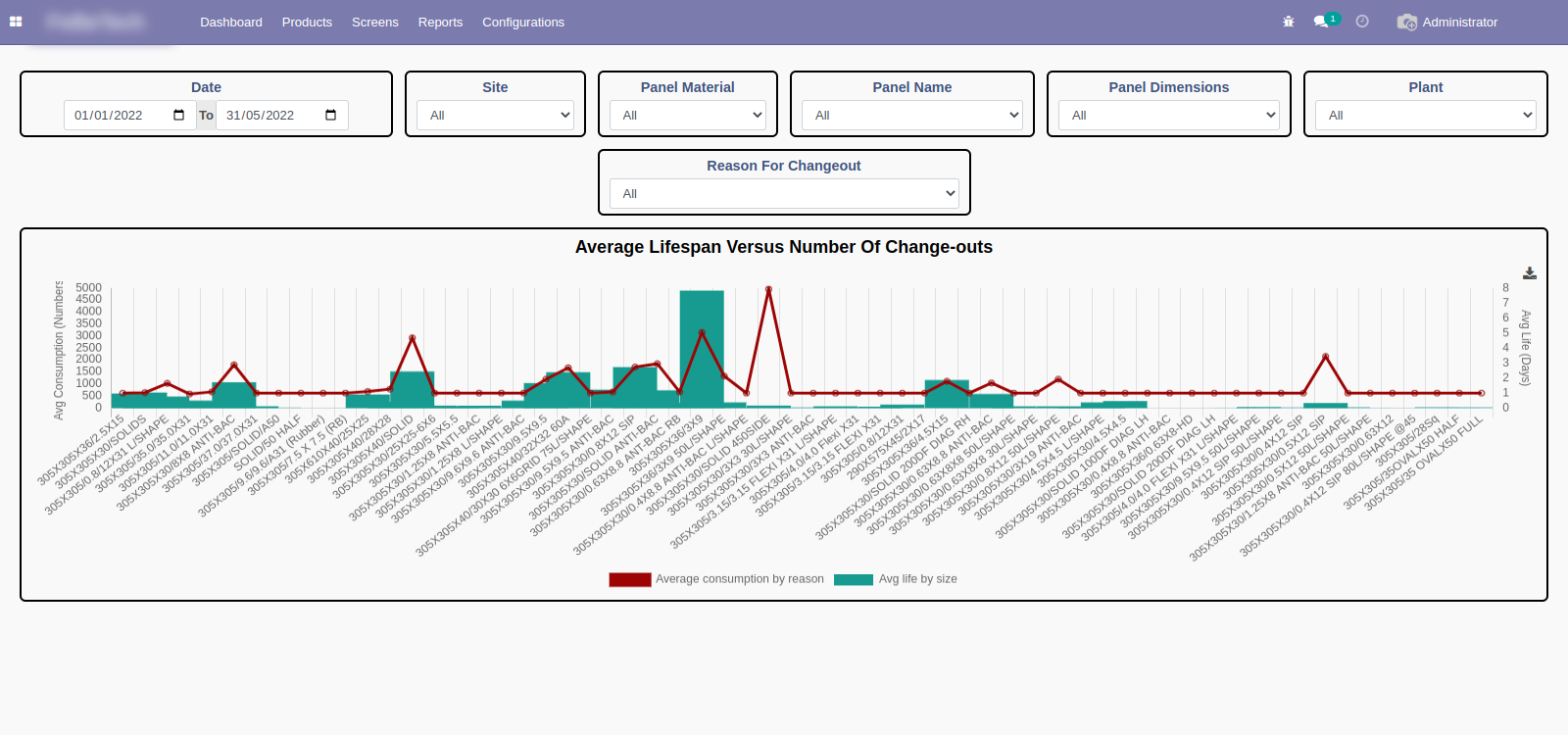
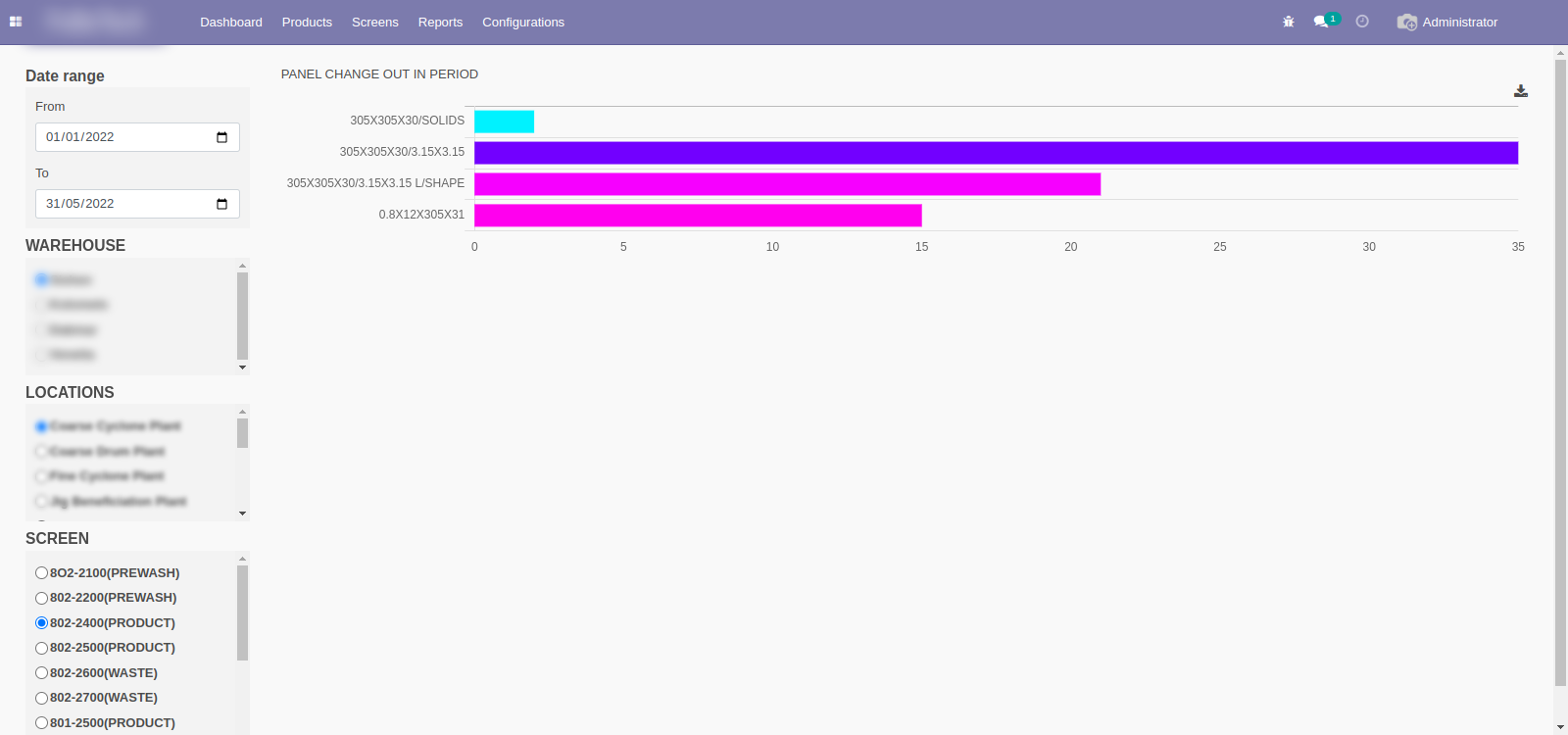
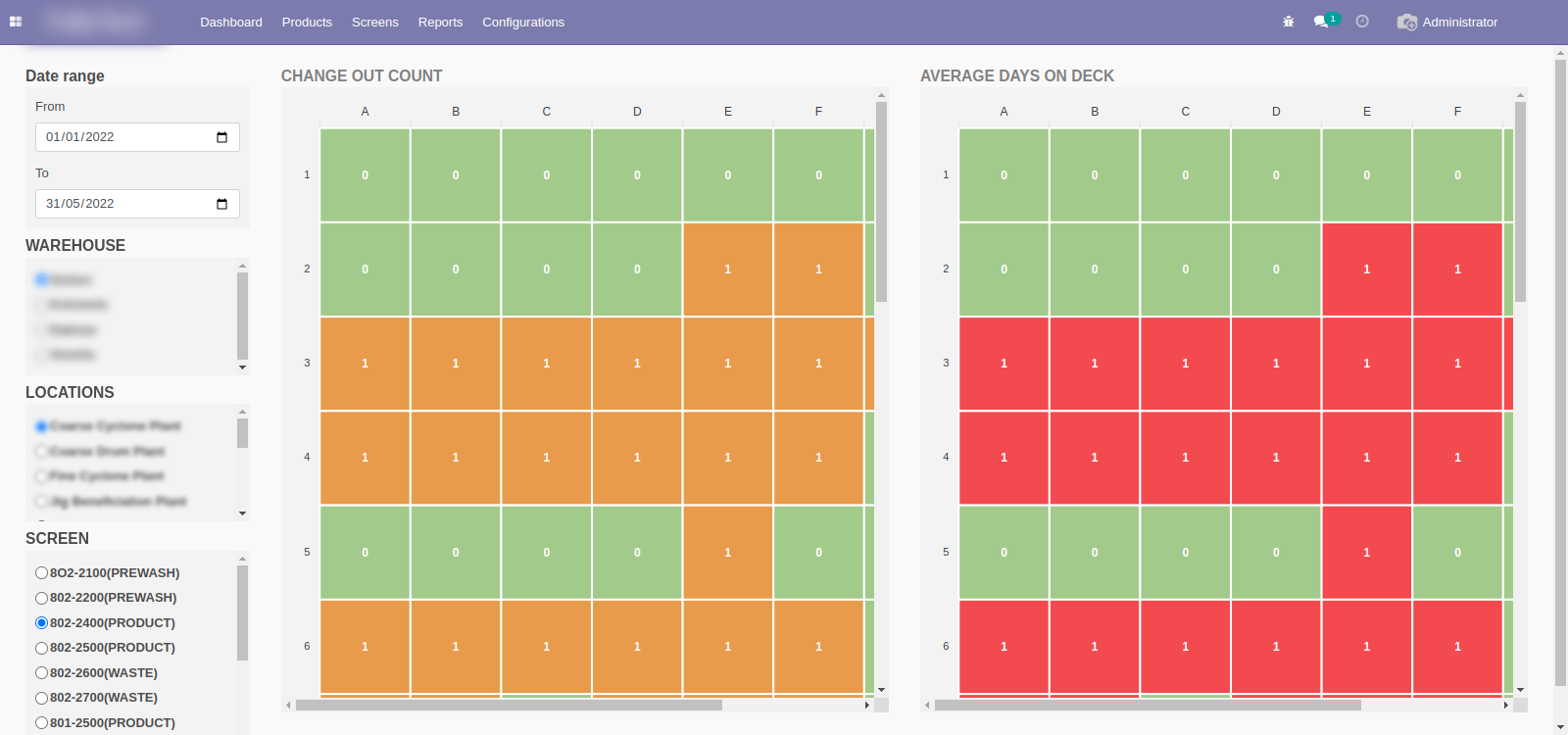
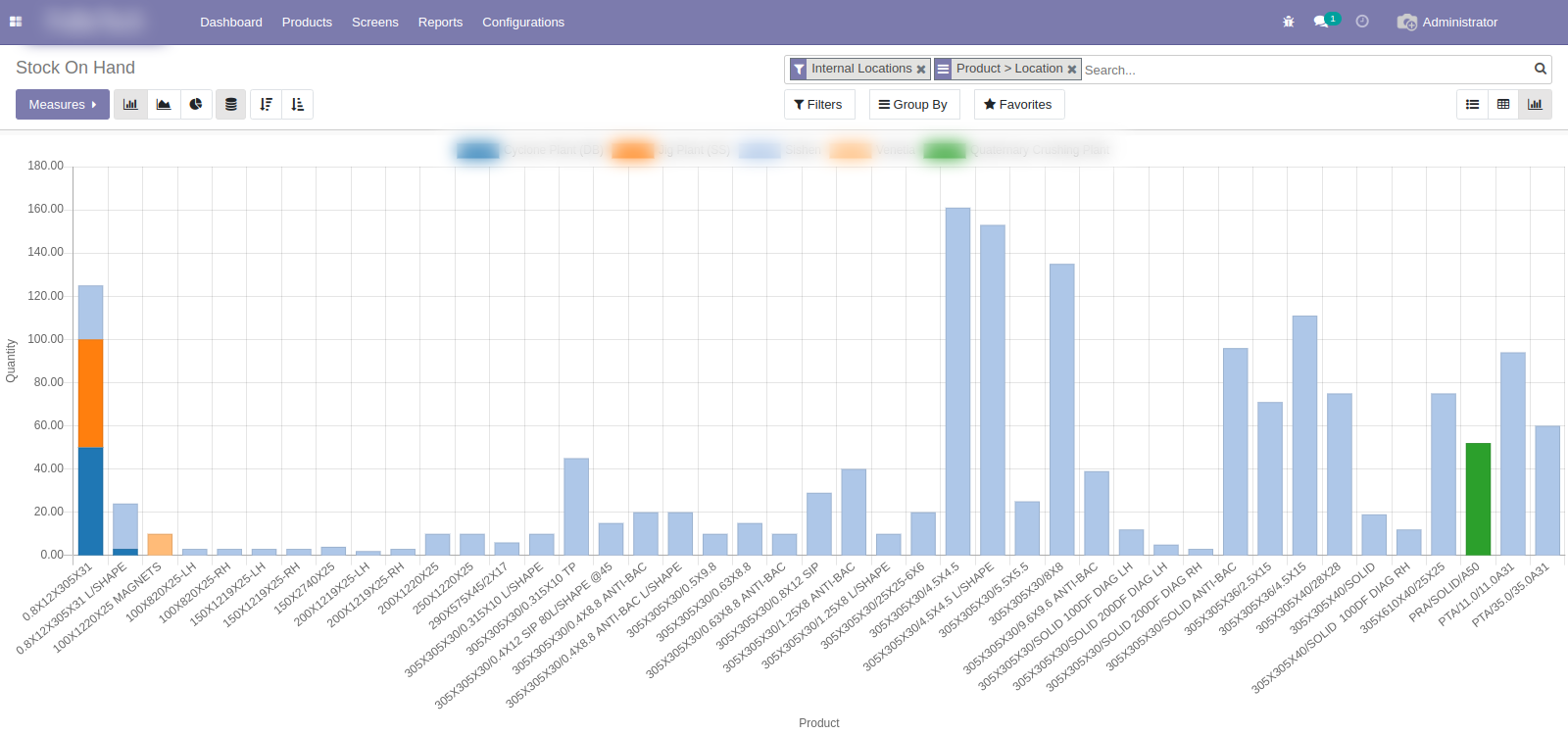
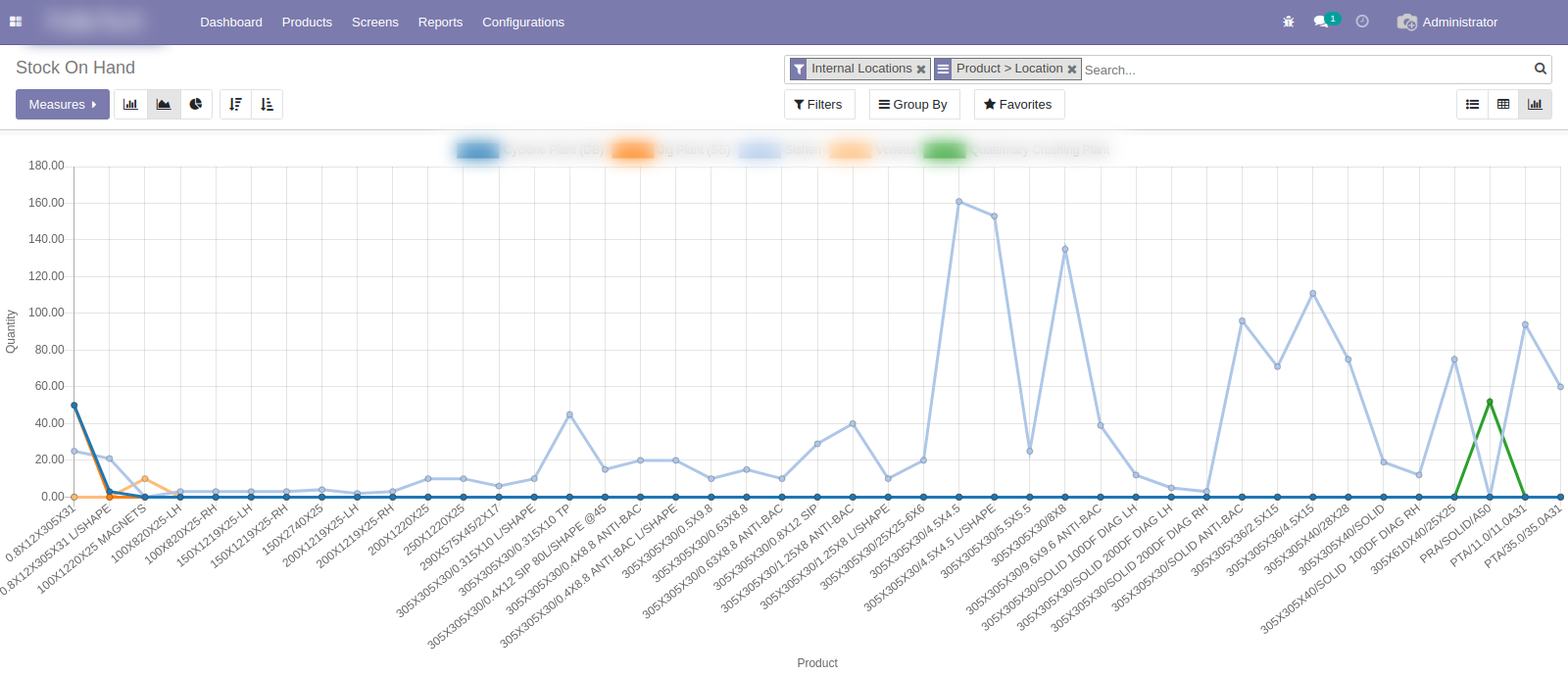
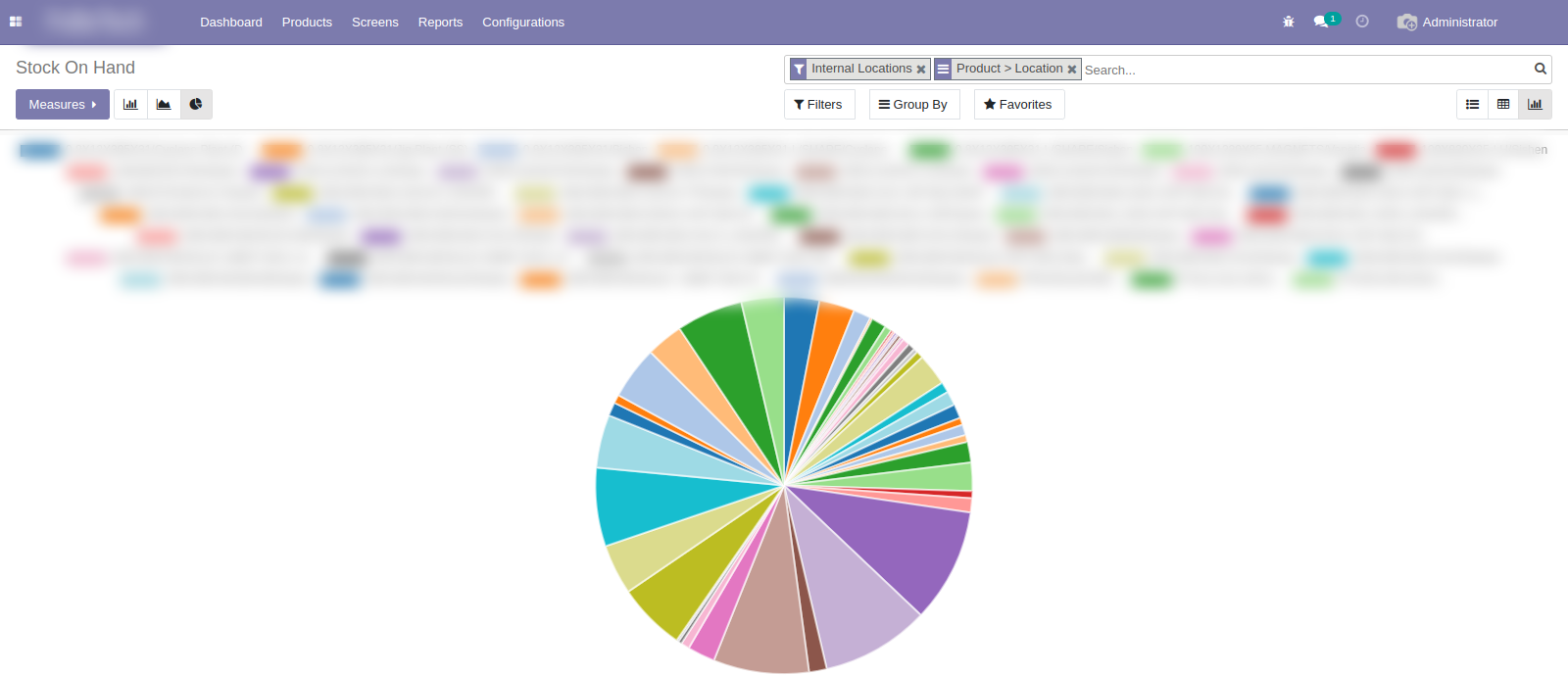